Your Material Handling Equipment requires regular maintenance to keep in good working order. When equipment is not maintained, it can run inefficiently, cause expensive and dangerous failures, and ultimately cost more to replace. Let’s break down how maintenance saves you money and extends the life of your equipment.
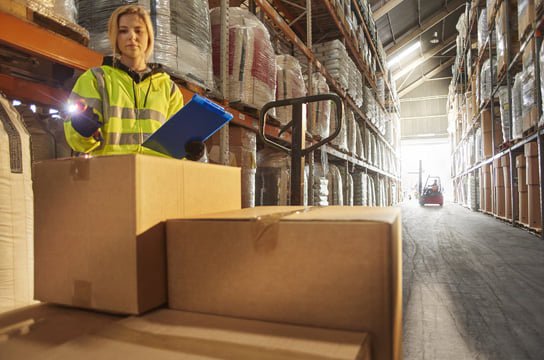
What is preventative maintenance?
Just as you should see your doctor regularly to keep healthy, or change the oil in your car, you should schedule your equipment for regular check-ups. This is called Preventative Maintenance (sometimes known as preemptive maintenance, protective maintenance, or scheduled maintenance). This will catch problems before they become costly. A proper examination will include checking fluids, replacing filters, cleaning components, blowing out dust and other contaminants that may be airborne in your warehouse, and assessing the wear of each part. This is the time to repair or replace parts that are getting worn before they break to avoid unplanned, catastrophic failure. These sudden, unexpected failures mean paying for rush repairs (or a new truck) and losing money in the downtime while the equipment is out of commission.
What is the cost of preventative maintenance?
Let’s consider an example using very generic pricing examples. Every application is different with unique truck types, intensity of use, and required maintenance intervals. But for demonstrative purposes, consider the following a general example of managing your fleet reactively when things break down compared to proactively instituting a consistent preventative maintenance program.
Let’s say you pay $40,000 for a new electric forklift and $0 in maintenance. If you only have your truck repaired when it breaks, here’s an example of how much that could cost you. Three years (6,000 hours) later, it breaks suddenly in the middle of a shift. The battery was running dry and it was being overcharged constantly, which caused it to overheat – the cards fail and then the drive motors fail. The cost of repairing the cards is $2,000 plus labor, a similar amount for the motors, plus a new battery at $6,000. You also lose $1,200 in productivity, paying the operator for 2 weeks during the downtime while you wait for the repairs. Total cost of ownership after 3 years: $51,200.
Let’s calculate how this plays out with a preventative maintenance program instead. You pay the $40,000 for a new truck. You pay $250 for preventative maintenance and some minor repairs four times per year. By the second year, the technician sees heat wear on the motor and corrosion on the battery. He diagnoses an underwatered battery. At no cost, you just have to start watering the battery every week. After 6,000 hours, you’ve only paid $43,000 for the truck and the maintenance program. On top of that, this healthy truck will last you at least 4,000 more hours with continued preventative maintenance.
Does preventative maintenance save money?
In our example, you could end up saving more than 15% if you have a preventative maintenance program. While those maintenance bills might look costly when they come in every quarter, it’s worth it in the long term. At Lift North America, not only is our preventative maintenance plan going to save you money, it will keep your equipment in better shape. Our technicians are trained on all makes and models, not just one brand. Just like a Ford needs different maintenance than a GM, a UniCarriers truck needs different maintenance from a Heli. Since we’re able to maintain all types of trucks, with our preventative maintenance plan you’ll save money, your equipment will last longer, and you’ll keep your operators happy. Give us a call or send us an email today to sign up.